In today’s modern workshops, electronic tools play a crucial role in maintaining and diagnosing vehicles. These tools, ranging from brake testers to gas emission analyser rely on accurate measurements to ensure safety and compliance. But how do we know they are really working accurately? The answer lies in proper calibration.
Why Is Calibration Important?
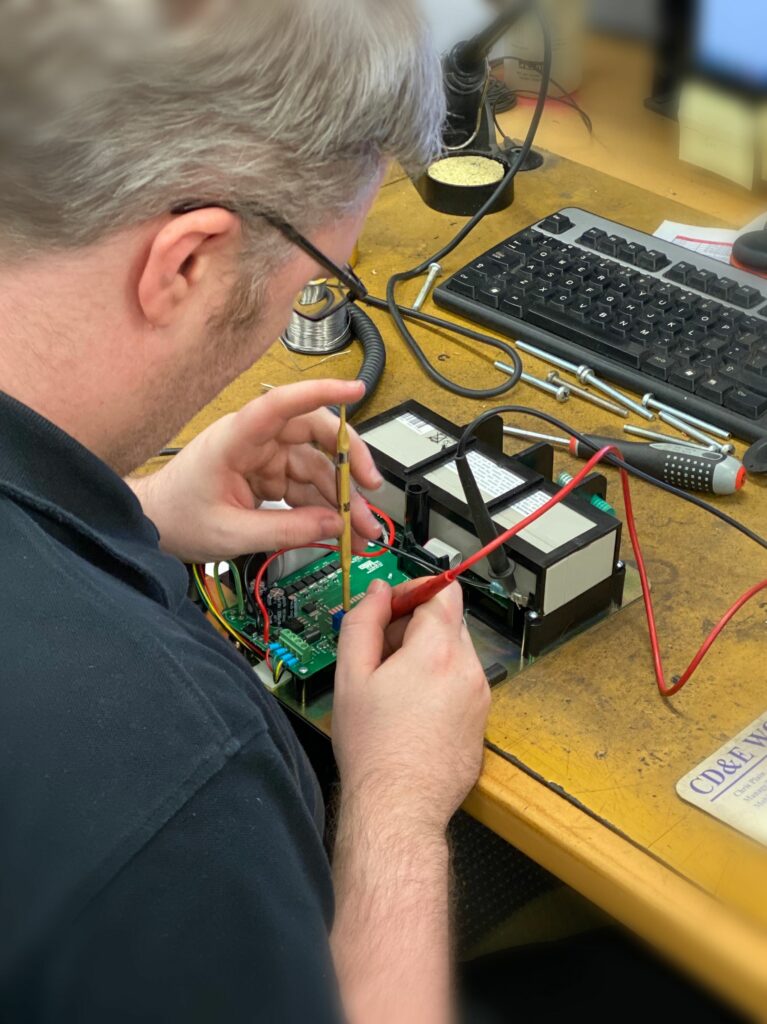
- Accuracy Degradation Over Time: All measuring devices, whether electronic or mechanical, experience accuracy degradation over time due to wear and tear. Additionally, external factors like electric or mechanical shocks and exposure to hazardous environments (such as oils or metal chips) can impact accuracy. Calibration helps correct any deviations within the instrument, ensuring precise results.
- Comparison with Known Standards: Calibration involves comparing the measurement taken by an instrument with a known standard. Ideally, the accuracy of the standard should be at least ten times better than that of the measuring device being tested. This comparison ensures that the instrument provides reliable data.
- Traceability and Reporting: Calibration not only checks accuracy but also establishes traceability. When an instrument is calibrated, a calibration laboratory provides a report showing the error in measurements before and after calibration. This documentation is essential for quality control and compliance.
When Should You Calibrate Your Measuring Device?
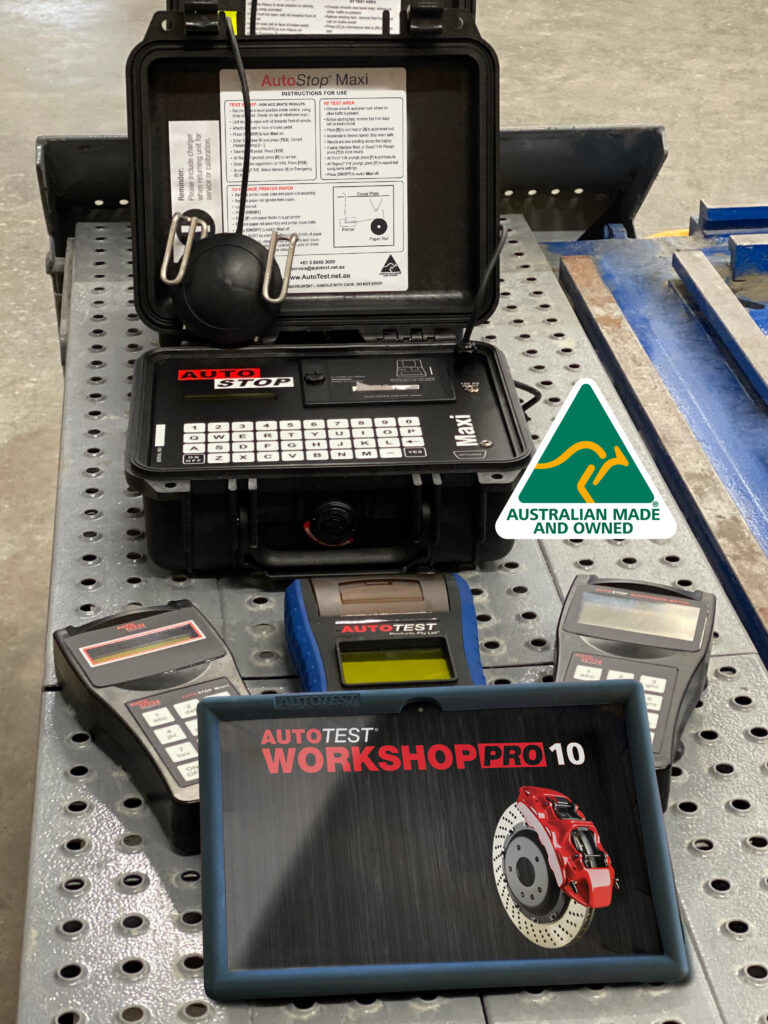
- Manufacturer’s Recommendation: Follow the manufacturer’s guidelines for calibration intervals. Some instruments may require annual calibration, while others need more frequent checks (quarterly or monthly).
- After Mechanical or Electrical Shock: Any significant shock (such as dropping the instrument) can affect accuracy. After such incidents, recalibration is necessary.
- Periodically: Regular calibration ensures consistent accuracy. Set up a schedule based on usage and environmental conditions.
Hidden Costs and Risks of Un-Calibrated Instruments:
The consequences of using un-calibrated measuring devices can be severe:
- Safety Risks: Incorrect measurements may lead to unsafe conditions.
- Legal Compliance: Roadworthy testing and other certifications require accurate instruments.
- Financial Loss: Errors can result in costly repairs or retesting.
Maintaining Standards and Certifications:
- Accredited Calibration Laboratories: Choose a calibration lab accredited by a recognized body (such as NATA in Australia). Accreditation ensures compliance with ISO 17025 standards.
- Guaranteeing Compliance: An accredited calibration lab provides confidence that your instruments meet industry standards. Compliance is essential for maintaining certifications.
Trust AutoTest:
- Australian Made and Owned: AutoTest Products, based in Kensington, Victoria, is an award-winning manufacturer and distributor of automotive testing and diagnostic products.
- NATA-Accredited Calibration Lab: AutoTest operates an ISO 17025-accredited calibration laboratory within its Kensington facility. All products are designed and assembled in Australia.
- Reliable Testing with Quality Components: AutoTest’s product range includes gas and opacity analysers, AutoStop brake-performance meters, suspension meters, sound level meters, and light transmission meters.